Search
mechanical and fluid systems
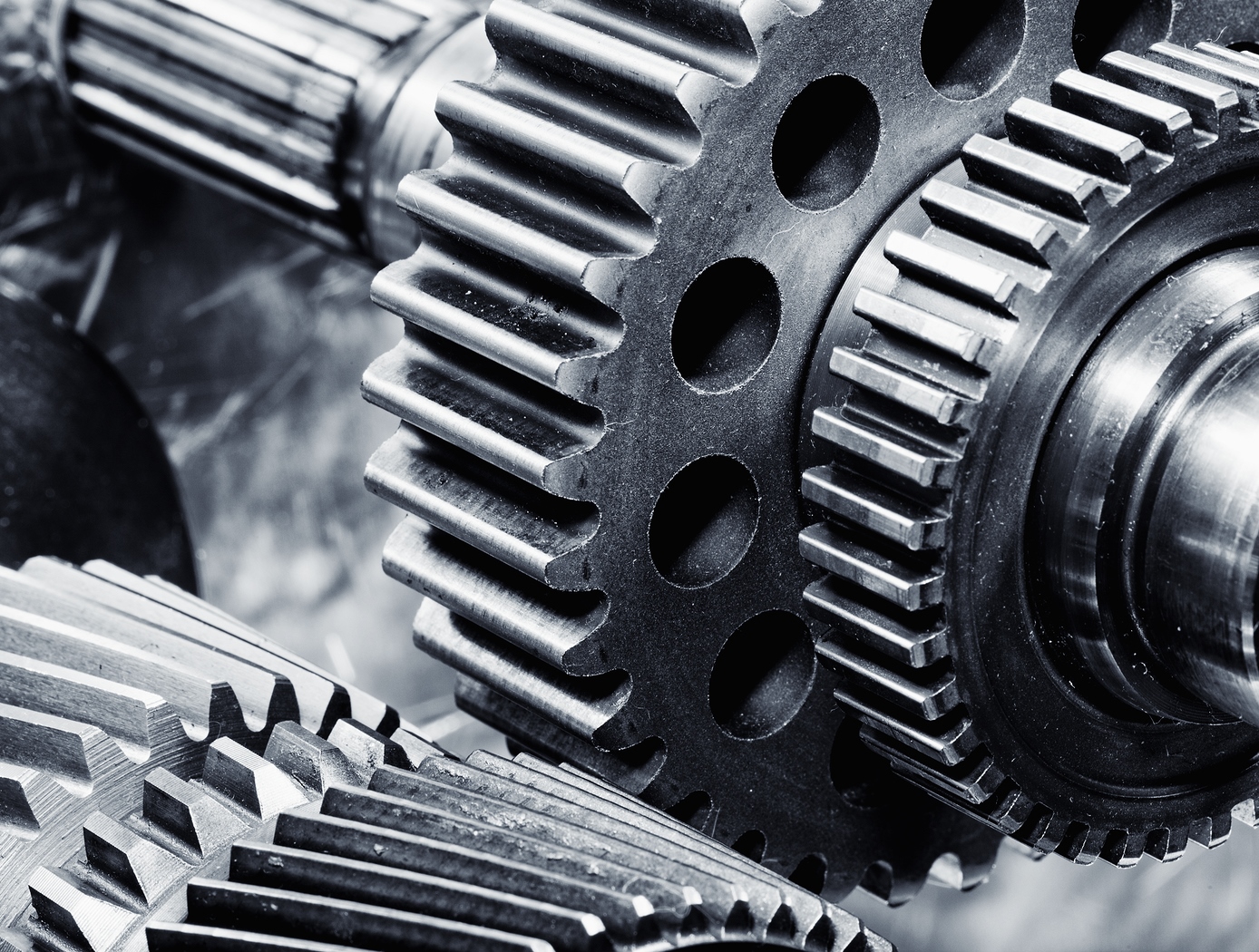
Gear Bearings
These patented gear bearings provide superior speed reduction in a small package. They form rolling friction systems that function both as gears and bearings and are compatible with most gear types, including spur, helical, elliptical, and bevel gears. These self-synchronized components can be in the form of planets, sun, rings, racks, and segments thereof. The design reduces micro chatter and eliminates rotational wobble to create smooth and precise control. It offers tighter mesh, more even gear loading, and reduced friction and wear.
Gear bearings eliminate separate bearings, inner races, and carriers, as well as intermediate members between gears and bearings. Load paths go directly from one gear bearing component to another and then to ground. By incorporating helical gear teeth forms (including herringbone), gear bearings provide outstanding thrust bearing performance. They also provide unprecedented high- and low-speed reduction through the incorporation of phase tuning. Phase tuning allows differentiation in the number of teeth that must be engaged govbetween input and output rings in a planetary gearset, enabling successful reduction ratios of 2:1 to 2,000:1. They provide smooth and accurate control with rifle-true anti-backlash. This produces a planetary transmission with zero backlash. The gear bearing technology is based on two key concepts: the roller gear bearing and the phase-shifted gear bearing. All designs are capable of efficiently carrying large thrust loads.
Existing gear systems have drawbacks including weak structures, large size, and poor reliability, as well as high cost for some types (e.g., harmon-ic drives). Gear bearings solve these problems with simpler construction, fewer parts, and superior strength.
By selecting the appropriate manufacturing method and materials, gear bearings can be tailored to benefit any application, from toys to aircraft.
Materials and Coatings
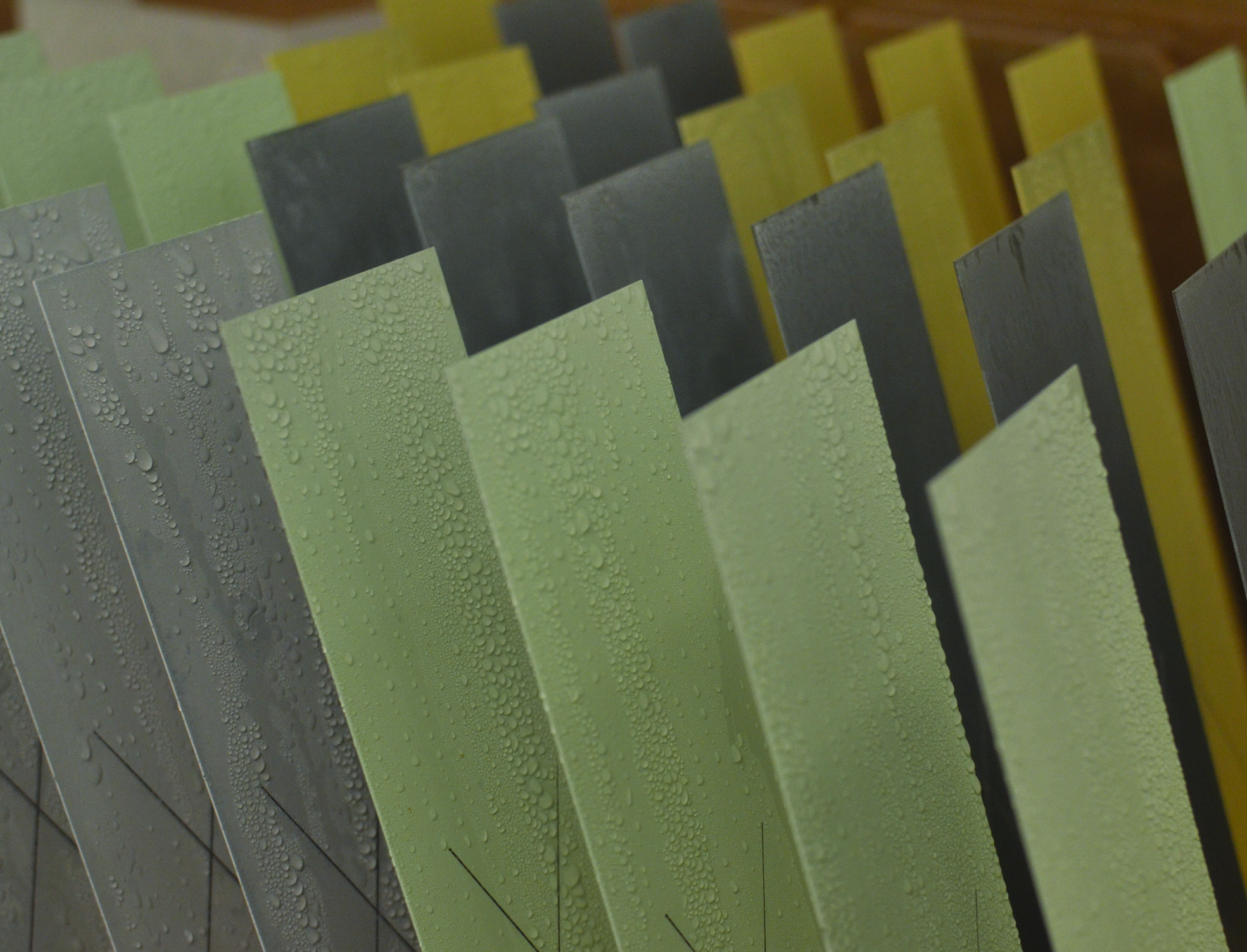
Smart Coating for Corrosion Detection and Protection
The smart coating is based on the controlled release of corrosion inhibitors and indicators from specially formulated microcapsules and particles pioneered by NASA (patent allowed). The coating detects corrosion in its early stages, inhibits it, and/or repairs the coating. The onset of corrosion triggers the release of compounds that indicate and inhibit corrosion. Mechanical damage to the coating triggers the release of film-forming compounds to repair the damage. In practice, the corrosion-responsive microcapsules detect the chemical changes that occur when corrosion begins and respond by releasing their contents. A corrosion indicator will identify the affected region with a color change, and healing agents and corrosion inhibitors help mitigate the corrosion.
The microcapsules can be tailored for incorporation into different coating systems. This multifunctional coating system will reduce maintenance cost and improve safety by preventing catastrophic corrosion failures. The coating can reduce infrastructure life cycle costs by extending the life of corrosion-susceptible structures and components, reduce inspection times of structures, and reduce the level of repair for corrosion-affected areas.